1.一種汽車凸緣零件技術要求
該凸緣零件的材料是40Cr,預備熱處理為調質,硬度260~300HBW;硬化層深為1.0~2.0mm;硬度為50~55HRC;金相組織為7~8級馬氏體;高頻感應淬火區(圖1中虛框線內)硬化層深1.0~2.0mm,為避免花鍵淬火裂紋,端面徑向硬化區域4~5mm(圖1中A端面)。
現行的機加工藝流程:毛坯退火→鉆孔→車小端外徑→車大端面至光潔、車內孔→車小端面→粗、精拉花鍵→車外圓、切槽→車、絞叉部孔→倒角→鉆螺紋底孔→攻螺紋→切卡圈槽→檢驗。
2.存在問題及注意事項
(1)帶凸緣的軸或軸頸,硬化區最好從凸緣根部R圓角處開始,以保證獲得最好的疲勞壽命。如根部不需要淬硬,硬化區距圓角處距離應為5~8mm,以避免過渡區的拉應力出現在應力集中部位。
(2)花鍵軸施行花鍵全長淬火時,硬化區應超過花鍵全長的10~15mm,即硬化區超過其應力集中部位。
(3)階梯軸的階梯小于3mm(D/2-d/2<3)時,允許采用同一感應器連續淬火,但不同直徑過渡時,零件在感應器內的移動速度應有所不同。
(4)當階梯軸的階梯大于3mm時,軸上的硬化區應分段處理。對疲勞強度要求較高的軸,其大小軸頸R圓角過渡處可采用滾壓或噴丸處理來改善和提高該處的疲勞強度。
綜上所述,圖1中不僅要求A端面淬火,同時要求A端面和臺階B處淬硬層連續成一體,對其感應器設計及淬火工藝調整有很大的難度,故進行了如下的工藝試驗研究。
3.工藝
(1)感應器及夾具設計??根據階梯軸的階梯(D-d)/2=(64-44)/2=10mm,則軸上的硬化區應分段處理,故設計成如圖3所示的分段式感應器,夾具設計如圖4所示。
(2)熱處理工藝??根據圖樣要求,凸緣淬火后的硬化層深為1.0~2.0mm,故選用的是中頻感應淬火機床,如圖5所示。
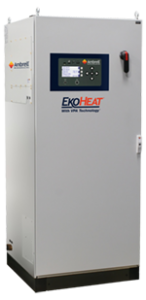
加熱電源參數:
頻率為25kHz;電壓:360-520,3 ph Vac,功率為100kW;淬火液流量為3.8~3.9m3/h;加熱時間為3.8s;噴液時間為6s;感應器與處理面間隙:距端面A為1mm。淬火后硬度為55~57HRC,試驗過程及金相取樣如圖6、圖7所示。
凸緣零件淬火后經磁粉探傷檢測,未發現缺陷磁痕顯示。
金相檢驗結果如圖8所示。
4.結果分析
(1)φ62mm軸頸3mm倒角處淬硬層為0.5mm(技術要求:1.0~2.0mm),不合格;從φ62mm軸頸下端15mm處淬硬層為2.4mm(技術要求:1.0~2.0mm),不合格。
由于該零件上同時有端面及凸緣兩個感應淬火疑難結構的存在,而上述部位的存在,在實施局部感應淬火時,易產生尖角效應,即在局部感應淬火時,位于尖角處的電流密集,易產生過熱或過燒現象,甚至產生淬火裂紋,故感應加熱工藝存在一定難度。
(2)由于φ62mm軸頸加熱溫度高,而φ62mm軸頸3mm倒角處加熱溫度低(加熱顏色偏暗),在感應器下端整體位置上移5mm,同時將φ62mm軸頸與感應器內壁處間隙加大1.5mm進行試驗,最終使問題得以圓滿解決(臺階處加熱時間由原來3.8s增加至4.2s)。
5.結語
(1)通過一發法感應器的設計,避免了凸緣處的電流密集導致過熱、過燒,甚至淬火裂紋的產生。?
(2)通過調整感應器間隙大小及加熱冷卻時間等工藝參數,使凸緣處感應淬火的淬硬層深度得到有效的控制,且淬硬層連續,分布均勻,繼而提升了淬火質量。
(3)通過定位夾具使凸緣的加熱位置得以控制,使其在感應淬火過程中旋轉定位加熱,進一步確保了淬火質量,且操作方法簡單可靠,易于實施,質量穩定,效率高,具有很好的應用價值。?
(4)程序編制合理,配合優化的工藝參數,滿足了凸緣所需的淬火硬度、淬硬層深度以及淬火均勻性,且淬火后變形小,達到了產品設計要求,提高了產品質量。