結合生產實際。分析了影響磨料用酚醛樹脂粘結劑粘度的幾個因素。結果表明,苯酚與甲醛摩爾比為1:1.15~1:1.16,氨水占苯酚的4.6%一4.9%,用40 min左右的時間使物料升溫至沸騰,后處理溫度不高于75時,反應過程平穩,反應周期適中,所得到的酚醛樹脂粘結劑的粘度較為適宜。
關鍵詞:酚醛樹脂;粘度;粘合劑
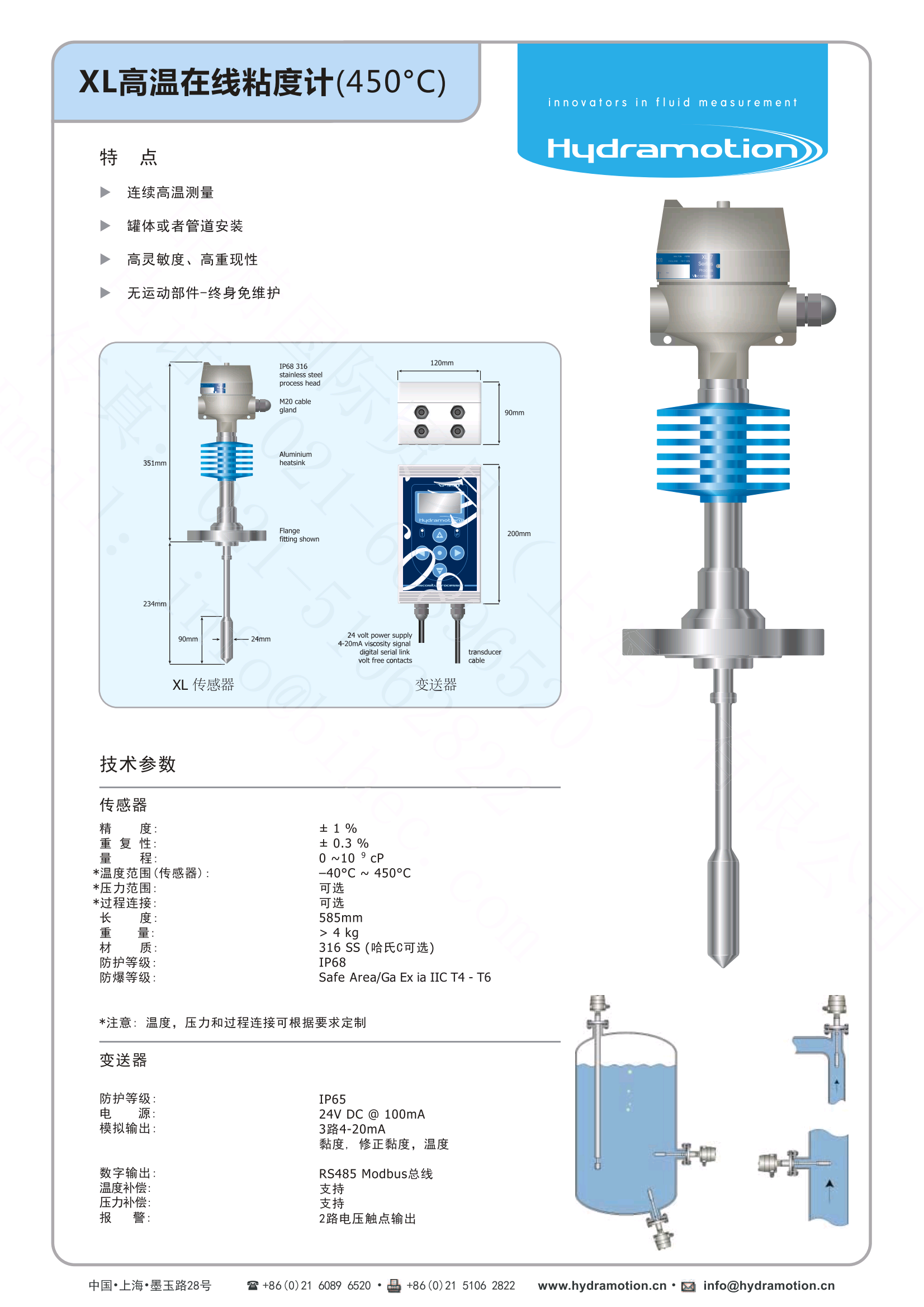
前言
酚醛樹脂具有良好的機械性能,耐熱性和加工成型性能,而且來源廣,成本低,廣泛用作砂輪的粘結
劑。酚醛樹脂液的粘度直接影響對磨料表面的浸潤均勻性。如果酚醛樹脂液粘度太低,物料流動性大,成型
性差.容易粘模,制成的砂輪機械強度差;如果粘度過大,對磨料表面浸潤性差,物料流動性差,混合不均
勻,不利于成型,制成的砂輪均勻性和機械強度也差。本文總結實際生產的經驗,分析了控制酚醛樹脂
結合劑的粘度的工藝方法,給出了適宜的工藝參數。
2試驗
以氨水作催化劑,在PH>7的條件下,加熱使苯酚和甲醛進行縮合反應生成甲階段的酚醛樹脂液。一
般應用廠家對樹脂液的技術要求如表1所示。但是在實際應用中發現,樹脂液的粘度在90~120 s時應用
效果最好。
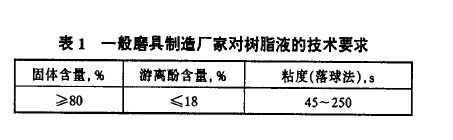
表2是通過實際生產中的數據,對苯酚甲醛比例、氨水比例、升溫速度、后處理最高溫度等因素對酚
醛樹脂液粘度影響的分析。
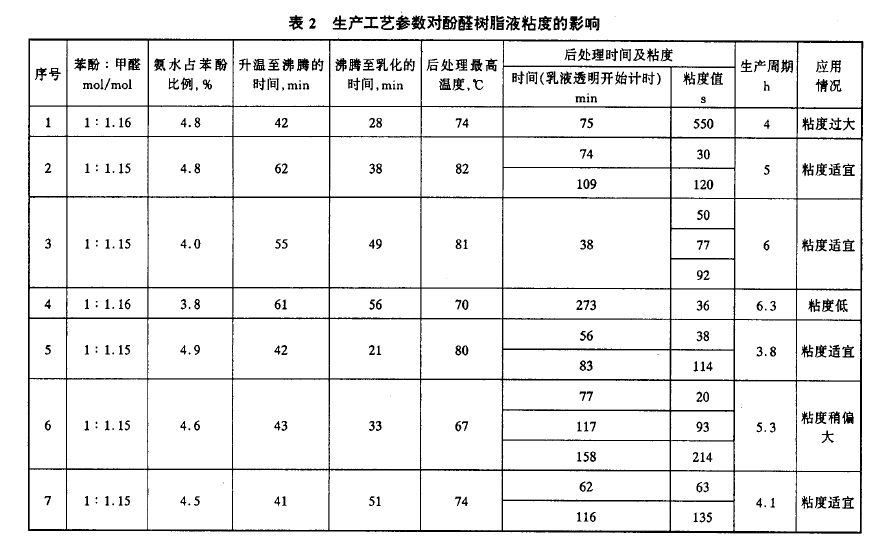
3、苯酚與甲醛比例對粘度的影響
隨著甲醛含量的增加,反應速度加快,粘度增長快。1號與2號相比較,1號的沸騰至乳化的時間相
對2號縮短了26%;物料透明后大約75min后測粘度,1號已經達到了550 s,而2號僅為30 s。苯酚與
甲醛摩爾比在1:1.15~1.16為宜。
3.2氨水的用量對粘度的影響
比較1號與4號、2號與3號可以看出。氨水比例大時粘度增長速度都快,所得樹脂的粘度也大。在苯
酚甲醛的摩爾比確定的情況下,可以通過增減氨水的用量來調整粘度的大小及反應速度的快慢。一般適宜
的氨水用量在4.6~4.9之間。
3.3升溫速度對粘度的影響
反應初期的升溫速度對反應速度和樹脂粘度有一定的影響。比較2號與5號,升溫速度慢反應平穩,
升溫速度快粘度增長快。這與升溫速度慢產生線性分子結構的樹脂含量較大,升溫速度快產生枝狀分子結
構的樹脂含量較大有關。升溫速度過慢生產工時增加,所以可以適當提高反應初期的升溫速度。一般控
制在40 min左右使物料沸騰為宜。
3.4后處理溫度對粘度的影響
在后處理階段,回升溫度對粘度的影響也很大。溫度越高,粘度增長越快,要嚴格控制回升溫度,防止
凝膠化。比較6號與7號,在物料透明后118 min后。后處理的溫度低的6號的粘度為93 s,而后處理的溫
度高的7號的粘度為135 s。一般后處理的回升溫度不能高于75為宜。
另外粘度中控合格后,需要將物料冷卻到一定溫度下放料,溫度過低時,粘度增大,流動性差,放料時
間增加,溫度過高,物料放出后在包裝桶內繼續反應,樹脂粘度繼續增大,甚至有凝膠化的可能。放料的溫
度不能高于40。
4結論
綜上分析,在產生砂輪粘結劑用酚醛樹脂時,適宜的工藝參數如下:苯酚與甲醛的配比在1:1.15~
1.16,氨水用量在4.6~4.9之間;物料沸騰時間控制在40 min左右,后處理的回升溫度不能高于75。
存貯的溫度不能超過25,貯存時間不能超過1個月。
